深澤直人氏をディレクターに迎え、2024年3月に発表された「WO Timeless standard collection」。このメディアを運営する、木を育てている会社ウッドワンがつくる、新シリーズが誕生しました。
これまで、木に携わるさまざまな職業の人へインタビューをする中で、木が持ついろんな個性と多様性を見つめてきましたが、「木」という自然美を好み、それを生業とするひとや企業には、どこか共通した考え、想いがあるように感じています。
今回は今一度原点に返り、このメディア運営を行う私たちの仕事、内側を見つめ、木を育てている会社のものづくりについて「WO ダブルオー」を通じて、一緒に想いを共有したいと思います。
WOブランドについてはこちら→“うぉぉー!”人生を豊かにする建材。
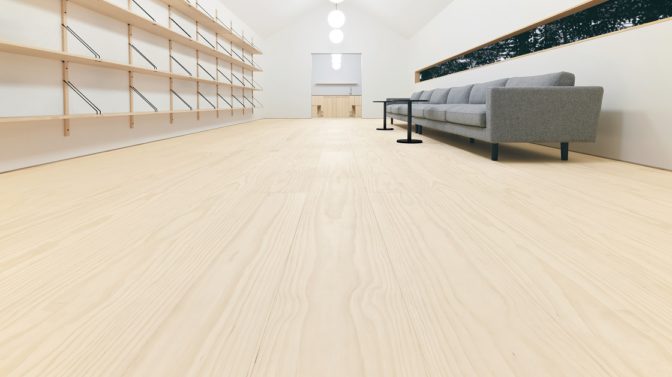
今回は創意工夫して入手した原木に、日本で最終商品として仕立てるまで。床材開発メンバーの代表8人に、開発秘話をお伺いしています。妥協せずに質の高いものを造りこむことが、開発の裏テーマでもあったといいます。
Nさん:前回の続きからいくと、角材のフリッチがJNL(ニュージーランドの現地法人Juken New Zealand Ltd. 以下、JNL)から入荷されて、そしてそれは乾燥された材料ではなく、木がもともと持っている水分を含んだままの「生材」という話でした。
床材工場で散水保管され、1.2㎜厚の単板にスライスしていき、含水率を調整しながら乾燥させていく…という流れです。
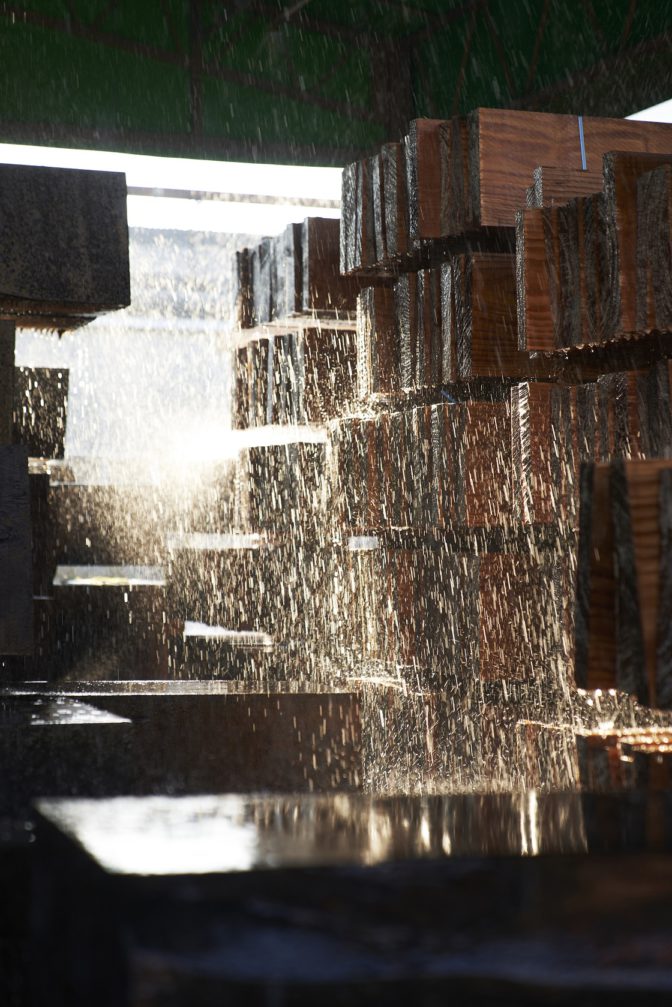
Iさん:スライスは、最初はヨコ(接線方向)でやろうって言ってましたよね。
Nさん:「板目」「突板1.2mm厚」はパイン材に限らず、今までやったことがなかったんです。真ん中(芯)を境に繊維方向が変わって逆目がおこるので、刃物が抜ける側の表面の肌が、荒れた状態になるんです。やはりヨコでは難しいなということで今はタテ(繊維方向)にスライスしています。
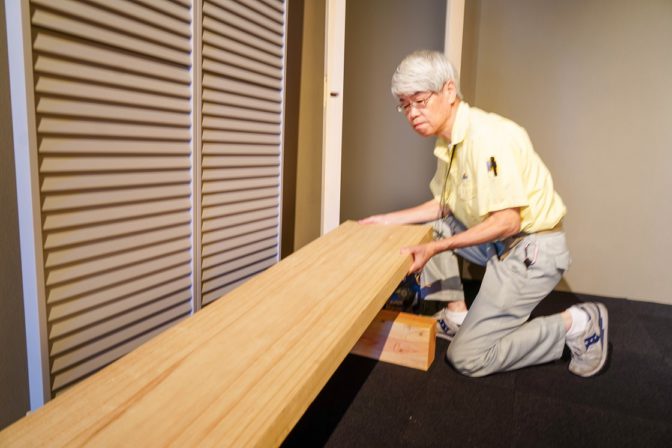
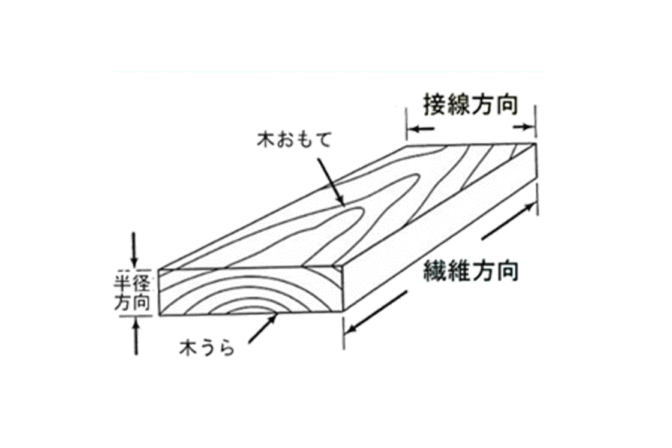
困っていることはありますか?
Nさん:生材を扱っているために、スライスしてみると中からアオ(カビ)や節、ヤニツボが出てくるとか…。表面は検品していますが、どうしても木の中からこのような木材の特性がでてくるんです。その材を短い材料として使っていこうか?補修しようか?着色しようか?現在はC1色(木の風合いを大切にしたウレタン塗装仕上げ)しかないですが、他にも色展開を考えようか…?今のところ、捨てたりはしていませんが、考えているところです。でもこの事実をJNLにフィードバックして、今ではだいぶ改善されていますね。
板目の浮造り(うづくり)
スライスした突板単板に、さらに浮造りをかける工程について教えてください。単板としては厚みがありそうですが、1.2㎜のものに浮造りの凹凸を表現するのはすごく難しそうです。
Fさん:まず「浮造り」というのは、木の表面に歯ブラシのようなブラシを回転させながらかけていくものなんですが、ブラシのメーカーさんに僕とメンバーでお伺いして、どういう条件にしたら板目の浮造りがきれいに出るのか、先方さんの協力もありながら条件の洗い出しをして探っていきました。それでブラシの痕が残るタテスジやヨコスジはある程度きれいにはなったんですけど、別の問題が出てきて…。
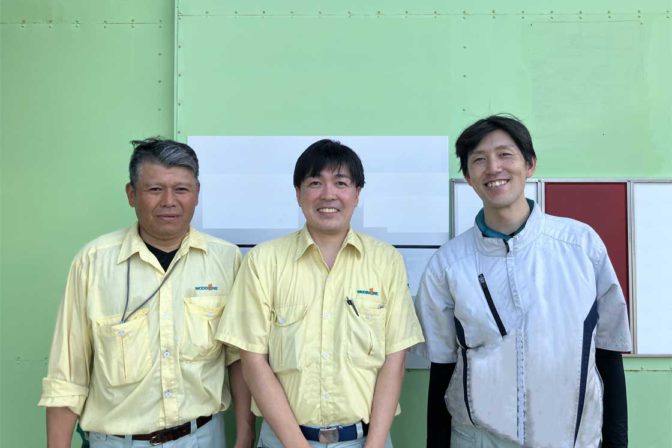
別の問題ですか。
Fさん:「浮造りが浅い」という問題がありました。今までずっとやってきたピノアースは柾目で、木目がまっすぐなのでブラシがかかりやすかったんです。板目はブラシに対して木目がナナメやヨコに入っていたり、単純に目の間が広かったりするので。
ブラシのメーカーさんでは、小さな設備、小さな材料で試験をしたので、実際に工場に戻って実物大でやると、やはり浅くなってしまって…。商品価値の担保としてはやっぱり浮造りの凹凸をしっかりかけたいと思いましたね。
Aさん:そう、実は1.2㎜の突板単板として確定する前は、「無垢」で浮造りの試作をしていて、無垢だったらけっこう簡単に浮造りがかかったので、単板でも簡単にかかると思っていたんです。でもいざやってみたらぜんぜんかからなくて、まったく違いました。突板単板の場合、プレス(圧力)かけるから?あの辺で変わったのかな。
Fさん:熱圧をかけることで圧縮され、高密度状態になったことで硬化したのかもしれませんね。そのあたりは無垢とは違ったのかもしれません。
床材工場のほうではどうでしたか?
Nさん:浮造りに関しては、既存商品に縁甲板フロングの松シリーズ、それも浮造り仕様のものがありますし、材料がもともとやわらかいのでなんとかなるかなと思っていたんです。でも実際に試してみると、タテスジ、ヨコスジ、浮造りのかかり具合が浅いところが出ましたね。
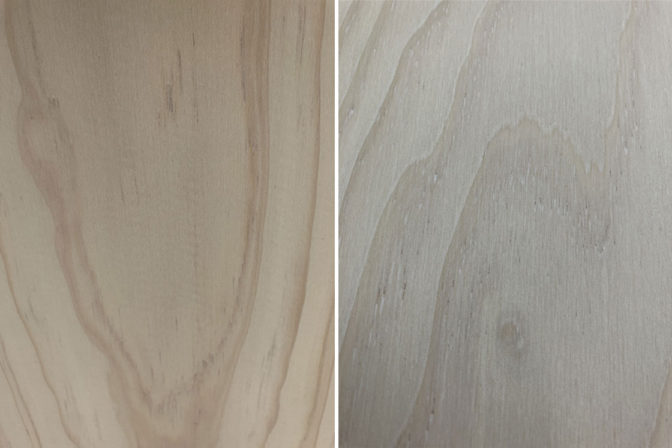
色々試した末に、ブラシの回転スピードを調整することで、ちゃんと凹凸が出るようになりましたね。フロングともブラシをかける回数を変えています。
Fさん:あと、ブラシの選定においても、フロングとWOでは材質を変えています。
Iさん:歯ブラシで、何度も強く磨いて血だらけになるのか、やさしくゆっくりていねいに磨くのか、というようなことですよね。
Nさん:その通りです。フロングの場合とは素材がちょっと違うのと、柾目と板目でも異なるので、今までとはやはり違いましたね。
板目のパイン、生材に浮造りをかけるときは、やさしく、ゆっくりかけないといけない?
Mさん:自然な浮造り仕上げを目指していましたが「やっぱり傷が入っちゃうのはよくないね」と品質管理のほうにも言われていましたし、床材工場で何度も試作していただいていましたが、傷がつくことをおそれすぎて弱すぎたりと、ずっと微調整がありましたね。
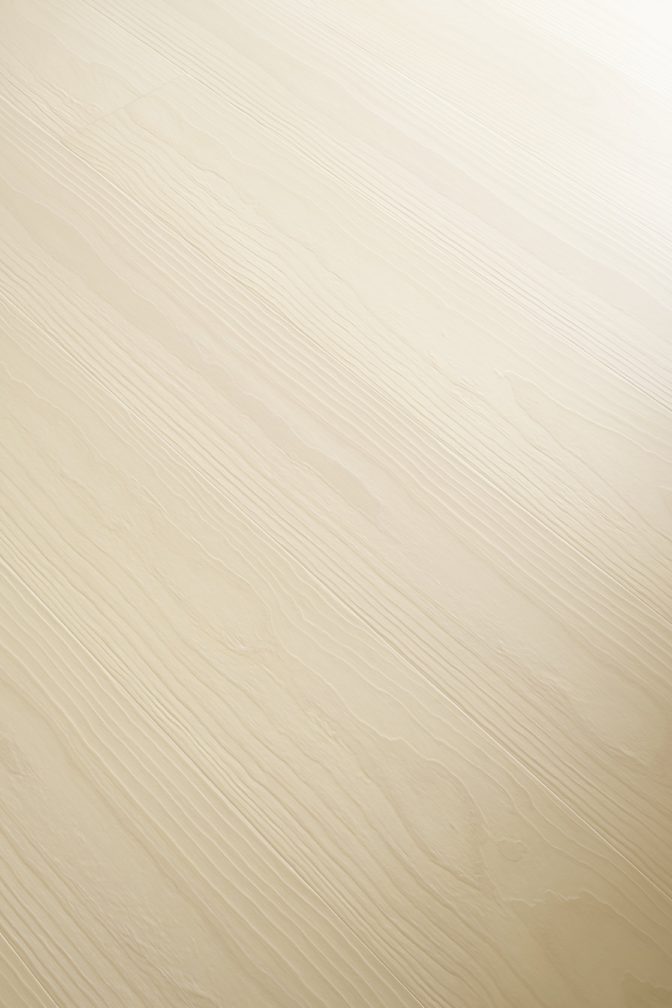
塗装
次に塗装仕上げについて教えてください。
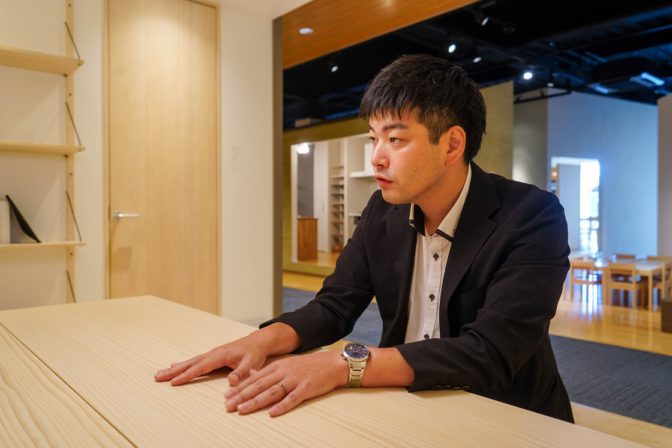
Mさん:色出しに関しても、床材工場で進めていただきました。今回目指していたのは“素地調の色”です。何枚も試験をして「いいね!」となったものの、小さいカットサンプルの状態でみると白くなりすぎていたり、空間全体でみると、やっぱりちょっと違っていたり。あとは屋外、屋内では見えかたが異なったりもするので…。今回は最初にルーム空間を作っていて、電球は柔らかいオレンジの光をだすものだったので、そことLEDと電球と…、もう全然違いましたね。本当に、床材工場に迷惑をかけながらですけど、僕は抽象的に「もうちょっと白く」とか、そんな指示しか出せなかったです…。
そういえば今回“素地調の色”“白”に決まった経緯はどのようなものだったのですか?
Iさん:これは、白くしようと言われたわけではなく、もともと素地で仕上げた塗装のサンプルをもっていたので、これを深澤さんにもっていったんです。すると「これは塗装しているの?してないの?これいいじゃない。こういう仕上げでいこう」という流れで決まりました。
色は、開発メンバー側から出たものだったんですね。
Iさん:なるべく素地のような、白木のように。塗装感を出さないように仕立てていきましたね。
Fさん:今回はほんとうに薄~く色が入ってるんです。色が薄いがためにちょっと調整したら色がガラッと変わってしまうので、製造担当者と塗装メーカーさんと、微妙な調整が大変でした。濃く塗りつぶすような色であれば木地の色を拾うこともなく、また少し色を足しても大きく変わることはありませんが…。
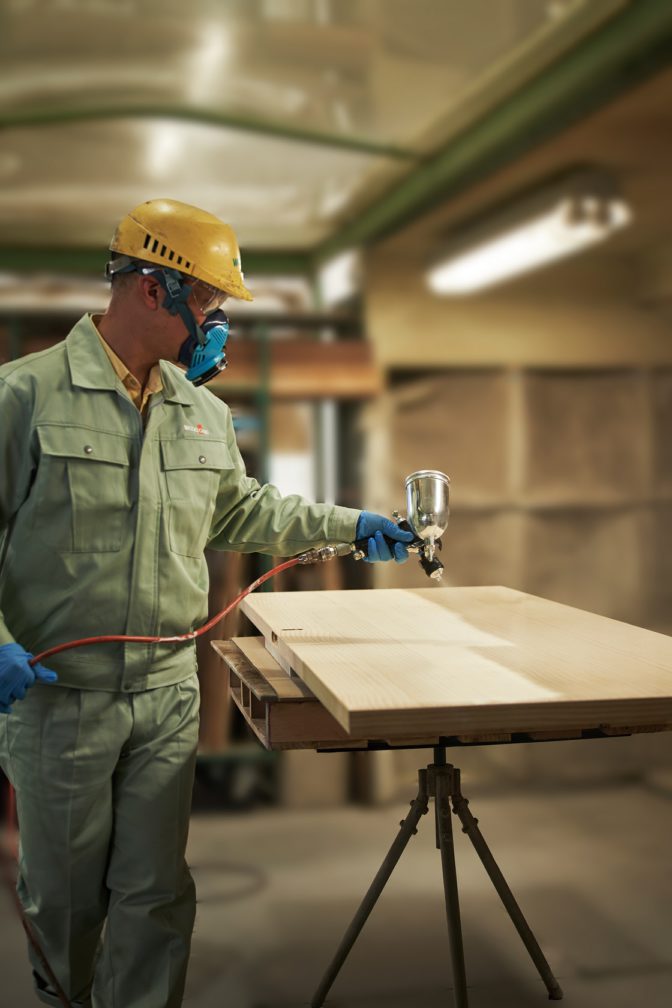
話は前後しますが、最初は「ドア」で話がすすんでいて、ドアの塗装は完全に手作業(手塗り)なんです。もちろん手作業だと綺麗に塗装できていたので、それを見本としてやるのは難しかったですね。「床」の場合は量が多く、さすがに手塗りでは追い付かないので、ライン生産方式で流していくやりかたです。
Mさん:一番最初に色を決めるときには、本社にある技術センターで手拭きで塗ってもらって、色合い、塗装の質感など、数パターン出してもらいましたね。
LED、電球、やわらかい光、太陽光…どの想定が正解?というわけではないんですよね?
Mさん:社内基準で言うと、色見用の光源は決まっていて社内ではそれでみるんですけど、やっぱり今回はルーム空間を組んでみたというところで、どちらも繰り返しみていましたね。社内基準はよかったけど、太陽光でみたら木目が活かせていないなとか、塗装感があるな、とか。工場で色出ししてもらうたびに、サンプルを数枚抱えて、みんなで外に行っては色の確認をしましたね。
Nさん:はい、色出しはたくさん、半年以上はやりましたね。当然、既存商品の生産稼働をしながらですので、その合間に調整していました。床材工場からはここ数年新商品がなかったので、「絶対ものにしないといけない」と思いながらやっていました。色の見本サンプルは手拭きで作成したもので、でも本当は工場の生産ラインでやらなきゃいけない。顔(表面)をつくっていくのが大変でしたね。浮造りの状態がいいか悪いかというところも仕上がりに左右されたりするので、いざ色出しする時によい状態のものが手元にあるかどうかというのも、微妙なところでした。
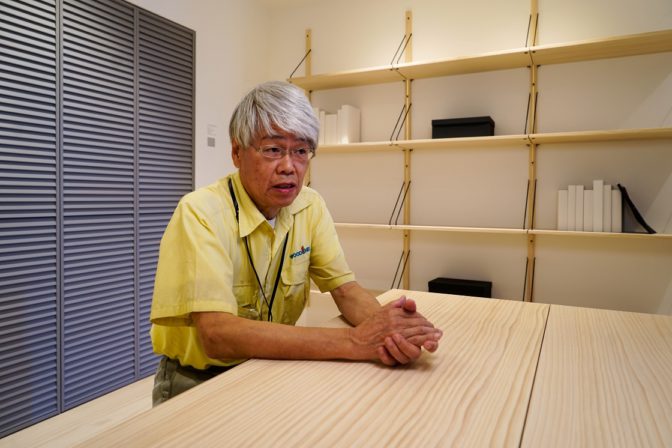
Hさん:「板目」だからですかね。一枚一枚顔が違うでしょ。硬いところ、木目が大きいところ。幅は303㎜、しかも長さは3mもある。面積も大きいので、色がのるところ、のらないところ。塗ってみてはじめてわかるんですね。品質的にそろえるのは厳しいものがありますよね。
生産に慣れるまでに、すごく時間がかかりそうですね。
Nさん:実は今もまだ苦労しているのが本音です。
Hさん:あと床材はここ(サイド)に面がついているんですよ。ただ面をとってあるという話なんですが、これ一つとるのも刃物が必要です。深澤さんが最終的に決めたのは1C(1㎜×1㎜)。それをとることによって部屋のなかで同化することなく、貼りあげたときにこれだけ迫力のある板だということがわかるんです。1.2㎜の突板といえども、実際には浮造りがあるのでここが薄くなっていたりして。面取りの苦労もありましたよね。
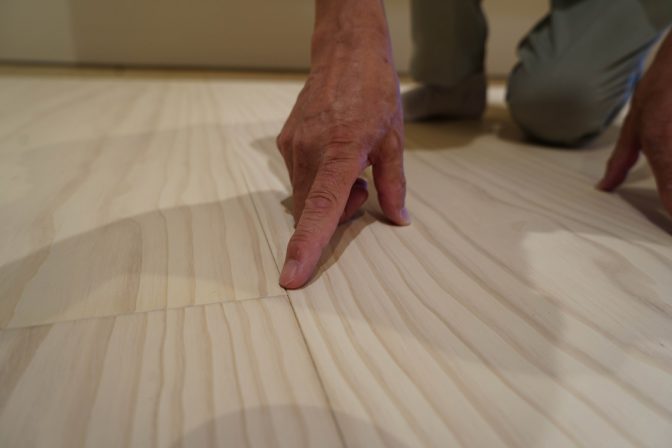
Nさん:そうですね、ぱっとできるものならいいんですけど刃物の設計の構成上、できなかったりもするので。
Hさん:当初0.7㎜で、という要求もあったりしたんですが、デザイナーさんというのは、そういうところまでこだわるんですね。けっこう地味なんですけど、床のデザインにおいては重要な部分だと思いましたね。
厳しい要求があったんですね。
Mさん:深澤さんは家具や家電製品など、様々な業界で実績を残されている方だからこそフラットな目線で、空間として、商品単品としての存在感というところでご指摘をいただけたと思うんです。その中の一部が床材の存在感を際立たせる、それが面形状であったりしたのかな。木材業界のあるある、じゃないですけど、こうやるべきという常識にとらわれずたくさん指摘をいただけて、今回は(床に限らず)僕らもすごく勉強になりました。
ちなみにですが、最終的に床材製品として仕上げるとき、この単板を貼るベニヤ基材についても、この長さと幅があるので、反り、狂いなどが起きないよう12パターンくらい想定して品質試験をして。調達と試作も大変でしたね。
次への展開
開発の“裏テーマ”でもあったという既存の商品の底上げ、レベルアップという点は、全体を通していかがですか?
Nさん:今回は、新しい設備を投入して今までにない仕様に挑戦しました。それに加えて人員のシフトの組み換えやイレギュラーな計画がけっこうありましたが、次の商品展開では、WOで経験させてもらったことが活きてくる気がしています。
Hさん:難題も多かったですが、社外の方が言うと、困難なことでもなんとかしよう、やってみようとなりますよね。善かれ悪かれ、技術が上がって「やればできるじゃないか」となり、そうやってアレルギーが消えていく。次にそういう案件があってもやれそうな気がしますよね。発表日や展示会日程が決まっていたので、本当に時間がない、という感覚にはなりましたが、結果深澤さんにも「いいものができましたね」と言われて報われました。
Nさん:深澤さんにできあがったものをみてもらうたびに課題が出て、まずこれならできるな、って自信を持てるものがあまりなかったんです。どうやって現場に落としていこうか、この提案はいつまでにできるだろうか、すごく不安でした。あとは、上層部からもWOに関しては妥協することのないようにと言われていたこともあり、工場としてはいつも最善を尽くすようにしていましたね。
Yさん:今のところ、作るたびにまだ課題が発生しています。まずは表面の仕上げ。単板それぞれ1枚ずつ顔が違うので、今までは数回かけて仕上がっていたものが、回数を増やしても仕上がらないこともある。木地(単板)の仕上げは一番重要だと思いますね。設備の維持管理を含め、品質を安定させて生産性をあげる。それを見極める目をもつこと…。たくさんの想いがつまっていますね。
床材が貼りあがった現場をみたとき、どんな気持ちでしたか?
Nさん:やっぱり綺麗だな、と思いました。WOシリーズのお披露目会でお客様に言われたのは、「これは無垢ですか?」ということ。そういうことを言われるとやっぱりうれしかったですね。まあ、さんざん1.2㎜厚の「突板」だって説明したあとでしたけど(笑)
Mさん:それはお客様によく言われますね。その評価は、床材工場のみなさんが本当に苦労された自然な浮造り仕上げ、塗りたくった感じではない塗装、質感からくるものだと思いますね。
商品企画室 I室長、Mプロダクトマネージャー、デザイン担当Hさん、品質管理部 兼 技術開発部 A部長、品質管理部 東海品質管理課 F係長、豊橋工場 Y次長、床材製造課 N課長、F班長(記事内では敬称略)お話、ありがとうございました!
「WO Timeless standard collection」特設サイトはこちら